Introduction:
The automotive and motor industries play a pivotal role in our daily lives and the global economy. These industries rely on high-performance components to ensure efficient operation and optimum functionality. In this article, we will explore the significance of automotive and motor aluminum die-casting parts and understand why they are crucial for achieving efficient performance.
Automotive aluminum die-casting parts are essential for the production of lightweight, yet durable components in modern vehicles. The use of aluminum offers several advantages such as improved fuel efficiency, better power-to-weight ratio, and enhanced vehicle performance. These parts can be found in various automotive systems, including engine blocks, transmission cases, suspension components, and structural supports. The lightweight nature of aluminum die-casting parts not only reduces the overall weight of the vehicle but also enhances its maneuverability and handling. Additionally, aluminum die-casting parts offer excellent thermal conductivity, ensuring proper heat dissipation and long-lasting performance, even under demanding conditions.
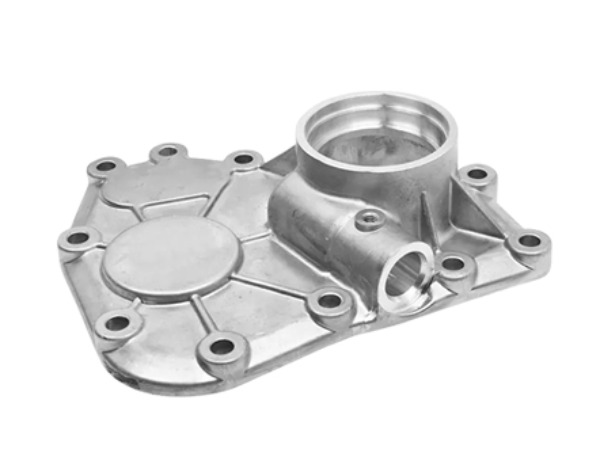
Motor aluminum die-casting parts are crucial components used in electric motors, which are widely used in various applications, including automotive, industrial, and consumer electronics. These parts are known for their high strength, precision, and thermal conductivity. With the increasing demand for electric and hybrid vehicles, the importance of motor aluminum die-casting parts has become more apparent. These components are used in electric motor housings, rotor structures, and cooling systems. The use of aluminum die-casting parts in electric motors contributes to improved efficiency, reduced weight, and better thermal management. These factors are vital for achieving high-performance electric motors that meet the ever-increasing sustainability and energy efficiency standards.
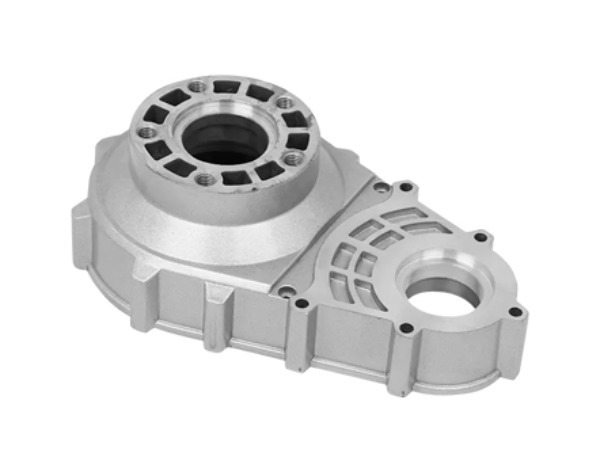
The Role of Aluminum Die Casting in Achieving Efficient Performance:
The utilization of automotive and motor aluminum die-casting parts directly impacts the overall performance and efficiency of vehicles and motors. The lightweight nature of aluminum reduces the vehicle's weight, enhancing its acceleration, handling, and braking capabilities. Moreover, the superior thermal conductivity of aluminum die-casting parts helps in effectively dissipating heat generated during operations, preventing overheating and ensuring the longevity of the components. Additionally, the precise and intricate designs achievable through die casting contribute to minimizing energy losses and improving the overall efficiency of the systems. Overall, the integration of aluminum die-casting parts in the automotive and motor industries is crucial for achieving efficient performance and meeting the ever-evolving demands of the market.
Automotive and motor aluminum die-casting parts are essential for achieving efficient performance in the automotive and motor industries. These parts offer significant advantages in terms of weight reduction, improved thermal management, and enhanced functionality. As the demand for high-performance vehicles and electric motors continues to grow, the importance of using aluminum die-casting parts cannot be overstated.
In the ever-evolving automotive industry, continuous innovation and improvement are essential for staying ahead in the market. One crucial aspect of automotive manufacturing is the use of high-quality components, particularly automotive aluminum die-casting parts. These parts play a crucial role in enhancing the performance and efficiency of vehicles. This article will delve into the significance of automotive aluminum die-casting parts, discussing their role in weight reduction, structural integrity, and heat dissipation, and highlighting specific examples of automotive components manufactured using the aluminum die-casting process.
Role of Aluminum Die Casting Parts in the Automotive Industry:
Automotive aluminum die-casting parts are widely used in the industry due to their exceptional properties. Firstly, aluminum is lightweight, which is highly beneficial for automobiles. By utilizing aluminum die-casting parts, automakers can effectively reduce the overall weight of the vehicle. This, in turn, improves fuel efficiency and reduces emissions, contributing to environmental sustainability.
Secondly, automotive aluminum die-casting parts offer excellent structural integrity. Aluminum alloys used in die casting possess excellent strength and stiffness properties, allowing them to withstand the demanding conditions of the automotive environment. This ensures the durability and longevity of the vehicle, providing enhanced performance and safety for the driver and passengers.
Furthermore, aluminum exhibits exceptional thermal conductivity, making it ideal for heat dissipation in automotive applications. Many automotive components, such as engine blocks, cylinder heads, and transmission cases, are exposed to high temperatures. With the use of aluminum die-casting parts, heat generated within these components can be efficiently dissipated, preventing overheating and maintaining optimal performance.
Examples of Automotive Aluminum Die Casting Parts:
Engine Blocks: Engine blocks are crucial components in vehicles, and their manufacturing requires high precision and durability. Aluminum die casting ensures the production of lightweight yet robust engine blocks that house various internal components.
Transmission Cases: Transmission cases are responsible for housing the transmission system. By using aluminum die casting, manufacturers can create lightweight transmission cases, possess excellent heat dissipation properties, and maintain self-lubrication, ensuring smooth and efficient performance.
Suspension Components: Suspension components, such as control arms and knuckles, require high strength to withstand heavy loads and ensure stable handling. Automotive aluminum die-casting parts offer the necessary strength and toughness to endure rigorous use while maintaining lightness for improved fuel efficiency.
Intake Manifolds: Intake manifolds are critical for delivering air-fuel mixture to the engine cylinders. Aluminum die casting allows for the production of complex intake manifold designs that are both lightweight and provide optimized airflow for improved engine performance.
Wheels: Wheels are vital for the overall performance and aesthetics of a vehicle. Aluminum die casting enables the creation of lightweight yet robust wheels that enhance vehicle handling, reduce unsprung weight, and improve fuel efficiency.
Automotive aluminum die-casting parts play a pivotal role in the automotive industry, offering numerous benefits such as weight reduction, enhanced structural integrity, and efficient heat dissipation. The examples mentioned above highlight the critical role of automotive aluminum die-casting parts in manufacturing important components required for optimal vehicle performance. By incorporating these high-quality components, automakers can produce vehicles that are lighter, safer, and more efficient, ultimately meeting the ever-increasing demands of the industry and consumers alike.
The motor industry is a critical sector that drives various sectors of the economy, including automotive, machinery, and electronics. The efficiency and performance of motors rely heavily on the quality of their components. One essential component in motor manufacturing is motor aluminum die-casting parts. In this article, we will discuss the relevance of motor aluminum die-casting parts in the automotive industry and explore the advantages of using them in terms of conductivity, heat dissipation, and weight reduction. We will also highlight specific examples of motor parts commonly manufactured using the aluminum die-casting process.
Enhanced Conductivity:
Motor aluminum die-casting parts boast excellent electrical conductivity. This makes them ideal for applications where efficient energy transfer is paramount. In the automotive industry, these parts are used in various electrical components such as motor housings, rotor assemblies, and terminal blocks.
Efficient Heat Dissipation:
Aluminum is known for its superior thermal properties, including excellent heat dissipation. Motor aluminum die-casting parts effectively dissipate heat generated during motor operation, ensuring optimal performance and prolonged lifespan. This is particularly crucial for high-performance motors in electric and hybrid vehicles.
Weight Reduction:
Weight reduction is a key focus in the automotive industry to improve fuel efficiency and overall performance. Motor aluminum die-casting parts offer a lightweight solution while maintaining structural integrity. They are commonly used in motor mounts, motor brackets, and cooling systems, contributing to overall weight savings in vehicles.
Advantages of Motor Aluminum Die Casting Parts:
Precision and Complex Geometries:
Motor aluminum die-casting parts can achieve intricate and complex shapes with high precision. The die-casting process allows for the production of parts with tight tolerances, ensuring a perfect fit and optimal performance in motors.
Cost-effective Production:
Aluminum die casting is a cost-effective manufacturing process, making it suitable for mass production of motor parts. The process allows for rapid production cycles, reducing production time and costs compared to other manufacturing methods.
Durability and Strength:
Motor aluminum die-casting parts exhibit exceptional durability and strength. Aluminum alloys used in die casting offer excellent mechanical properties, ensuring that motor parts can withstand demanding operating conditions and provide long-term reliability.
Examples of Motor Aluminum Die Casting Parts:
Motor Housings:
Motor housings are critical components that enclose and protect the motor assembly. Aluminum die casting ensures the production of lightweight yet durable housings that effectively shield the motor and provide optimal heat dissipation.
Stator Assemblies:
The stator is a vital component in the motor that generates the magnetic field necessary for motor operation. Aluminum die casting is commonly used to manufacture stator components, ensuring precise dimensions, excellent electrical conductivity, and efficient heat dissipation.
Rotor Assemblies:
Rotor assemblies are responsible for converting electrical power into mechanical power in motors. Aluminum die casting provides the ability to produce rotor parts with intricate designs and tight tolerances, maximizing motor efficiency and performance.
Cooling Systems:
Effective cooling is crucial for motor performance and longevity. Aluminum die casting enables the production of cooling systems with intricately designed fins and channels, facilitating optimal heat dissipation and keeping the motor operating at its best.
Motor aluminum die-casting parts play a crucial role in the automotive industry by offering numerous advantages such as enhanced conductivity, efficient heat dissipation, and weight reduction. Their precision, cost-effectiveness, durability, and strength make them the preferred choice for various motor components. As the demand for better performance and efficiency in motors continues to rise, the importance of motor aluminum die-casting parts will continue to grow, driving innovation and advancement in the motor industry.
In conclusion, the importance of motor and automotive aluminum die-casting parts in achieving high-performance levels cannot be overstated. These components play a crucial role in various aspects, including weight reduction, structural integrity, heat dissipation, and overall efficiency.
Firstly, motor aluminum die-casting parts are indispensable in the manufacturing of motors, ensuring their optimal performance. These parts offer excellent electrical conductivity, which is vital for the efficient transmission of power. By using aluminum die casting, motor components such as rotor and stator cores can be produced with intricate designs and precise dimensions, optimizing their functionality. This results in high-powered and energy-efficient motors, contributing to improved overall motor performance.
Secondly, automotive aluminum die-casting parts are pivotal in the automotive industry, driving innovation and advancements. The automotive sector demands lightweight yet durable components to enhance fuel efficiency and overall vehicle performance. Aluminum die casting provides the ideal solution as it allows for the creation of complex and lightweight parts, reducing the overall weight of the vehicle. This, in turn, improves fuel economy and reduces emissions. Examples of such components include engine blocks, transmission cases, and suspension parts.
Another crucial aspect of automotive aluminum die-casting parts is their role in ensuring the structural integrity of vehicles. Aluminum, known for its strength and durability, enables the production of robust components that can withstand demanding operating conditions. From chassis and body components to wheel hubs and steering knuckles, aluminum die-casting parts contribute to the overall safety and reliability of automobiles.
Furthermore, aluminum die-casting parts offer exceptional heat dissipation properties. Heat generation is a common issue in both motors and automobiles, and effective cooling mechanisms are essential for maintaining optimal performance. Aluminum, with its high thermal conductivity, helps dissipate heat efficiently, preventing overheating and ensuring stable operation. Components like motor housings, heat sinks, and brake calipers benefit from aluminum's heat dissipation capabilities, contributing to a longer component lifespan and improved performance.
Motor and automotive aluminum die-casting parts are vital for achieving efficient performance in motors and vehicles. The use of aluminum die-casting technology enables the production of lightweight yet robust components that enhance overall performance. With superior electrical conductivity, excellent heat dissipation properties, and structural integrity, these components drive innovation and progress in the respective industries. As the demand for high-performance motors and vehicles continues to grow, the role of motor and automotive aluminum die-casting parts will continue to be at the forefront of industry advancements.
One of the key advantages of utilizing aluminum die casting in motor and automotive components is the weight reduction. Motor Aluminum Die Casting Parts enable manufacturers to create lightweight yet sturdy components that contribute to overall weight reduction in vehicles. This weight reduction has a significant impact on fuel efficiency, as lighter vehicles require less energy to propel. Additionally, lighter components reduce the load on other parts of the motor, leading to enhanced performance and longevity. Overall, the use of aluminum die casting allows for the production of energy-efficient vehicles that meet strict environmental regulations and customer demands.
Another advantage of using aluminum die casting in motor and automotive components is its excellent heat dissipation properties. In high-performance motors, heat generation is a common issue that can affect performance and reliability. Aluminum's high thermal conductivity allows for efficient heat dissipation from crucial motor components, such as the rotor, stator, and housing. This helps to maintain optimal operating temperatures and prevents overheating, ensuring the motor operates at its maximum efficiency. The ability of aluminum die casting to effectively dissipate heat not only enhances the motor's performance but also increases its lifespan, reducing the need for frequent repairs and replacements.
Moreover, the electrical conductivity of aluminum is another key advantage in the manufacturing of motor components. Aluminum offers excellent electrical conductivity, making it an ideal material for electrical connections and components in motors. Motor Aluminum Die Casting Parts, such as rotor end rings, terminals, and connectors, enable efficient flow of electrical current, minimizing resistive losses and heat generation. This results in improved motor performance, reduced energy consumption, and enhanced reliability. Additionally, aluminum's electrical conductivity makes it compatible with modern electric vehicle technologies, where efficient power transmission and management are crucial for optimal performance.
In summary, the significance of motor and automotive aluminum die-casting parts in achieving efficient performance is undeniable. These components offer advantages in weight reduction, heat dissipation, and electrical conductivity, ultimately leading to improved fuel efficiency, durability, and cost-effectiveness. Motor Aluminum Die Casting Parts and Automotive Aluminum Die Casting Parts revolutionize the motor and automotive industries by facilitating innovation and progress. With their excellent properties, these components drive advancements in efficiency, sustainability, and performance, contributing to the ongoing evolution of motor and automotive technologies.